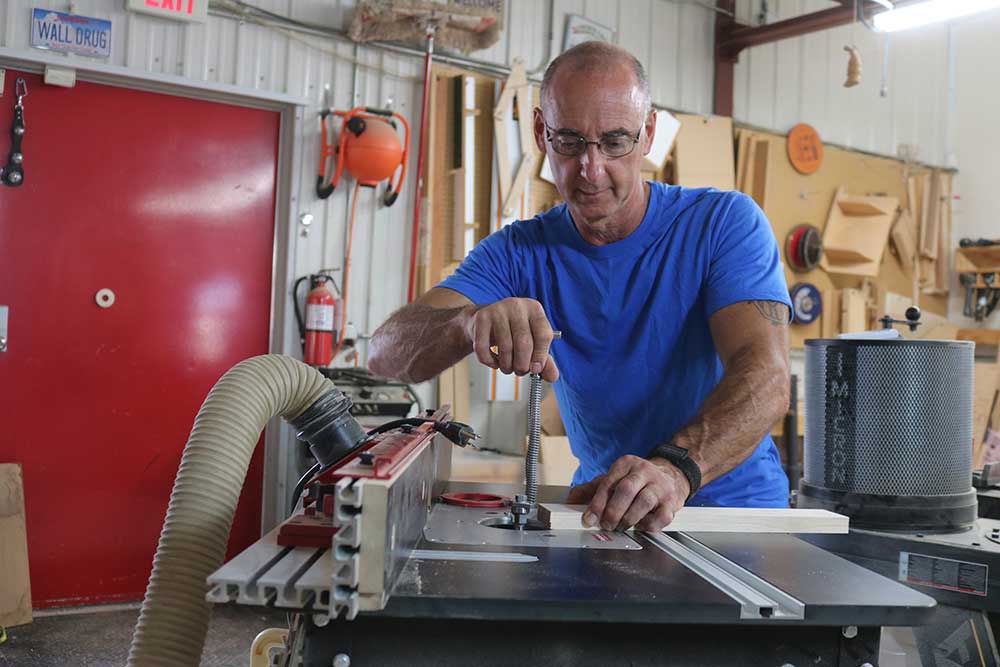
Build a Cordless Tool Station
George Vondriska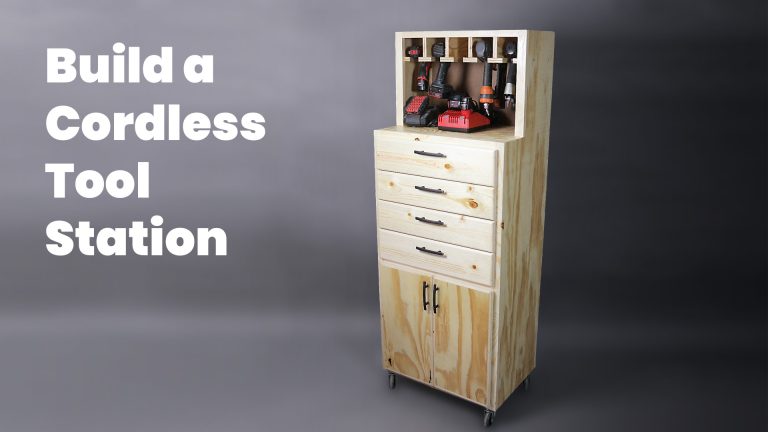
- In-depth Instruction; over 100 mins
- On-demand video access anytime
- Bonus downloadable PDF resources
- Access to class Q&A
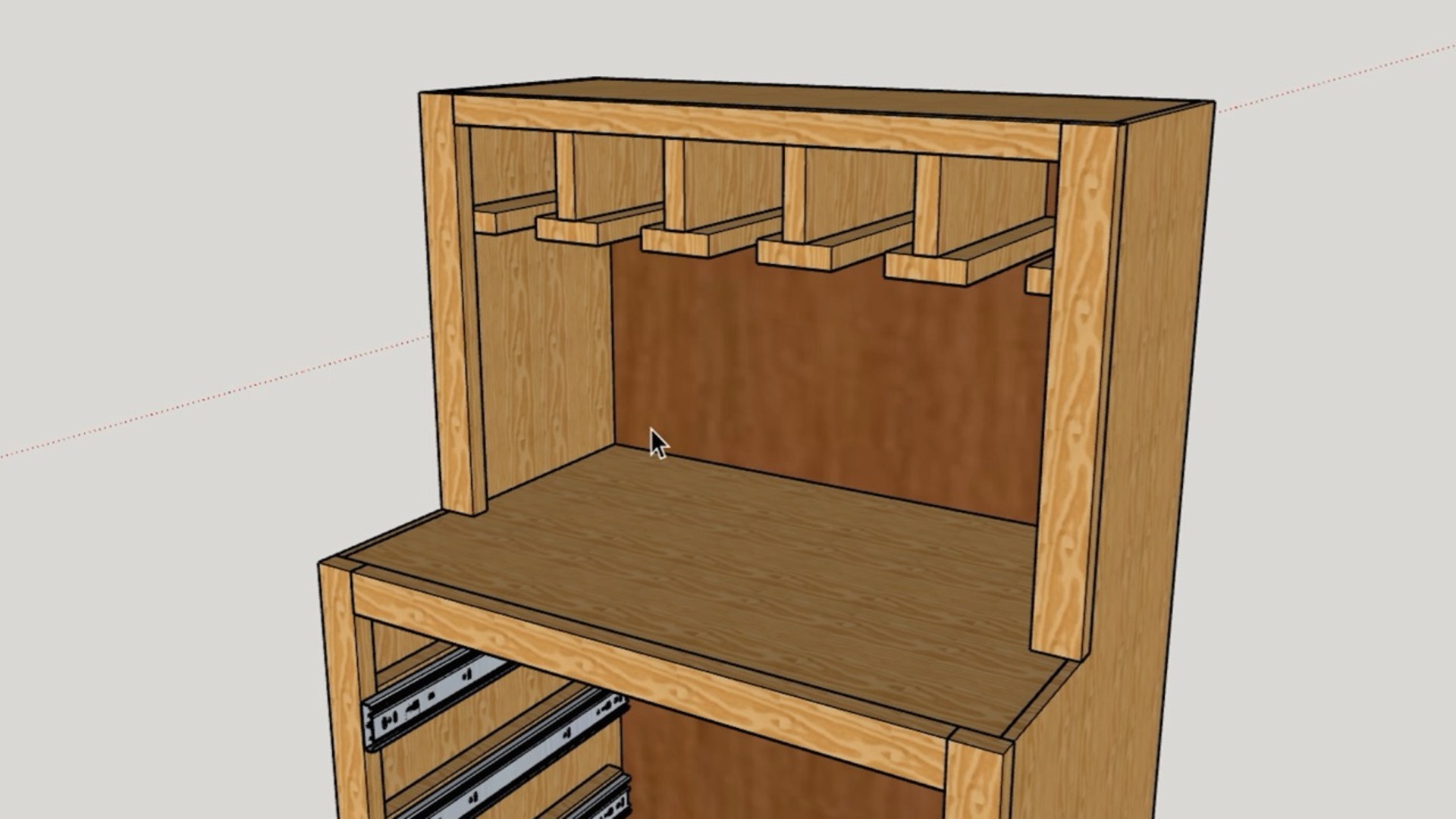
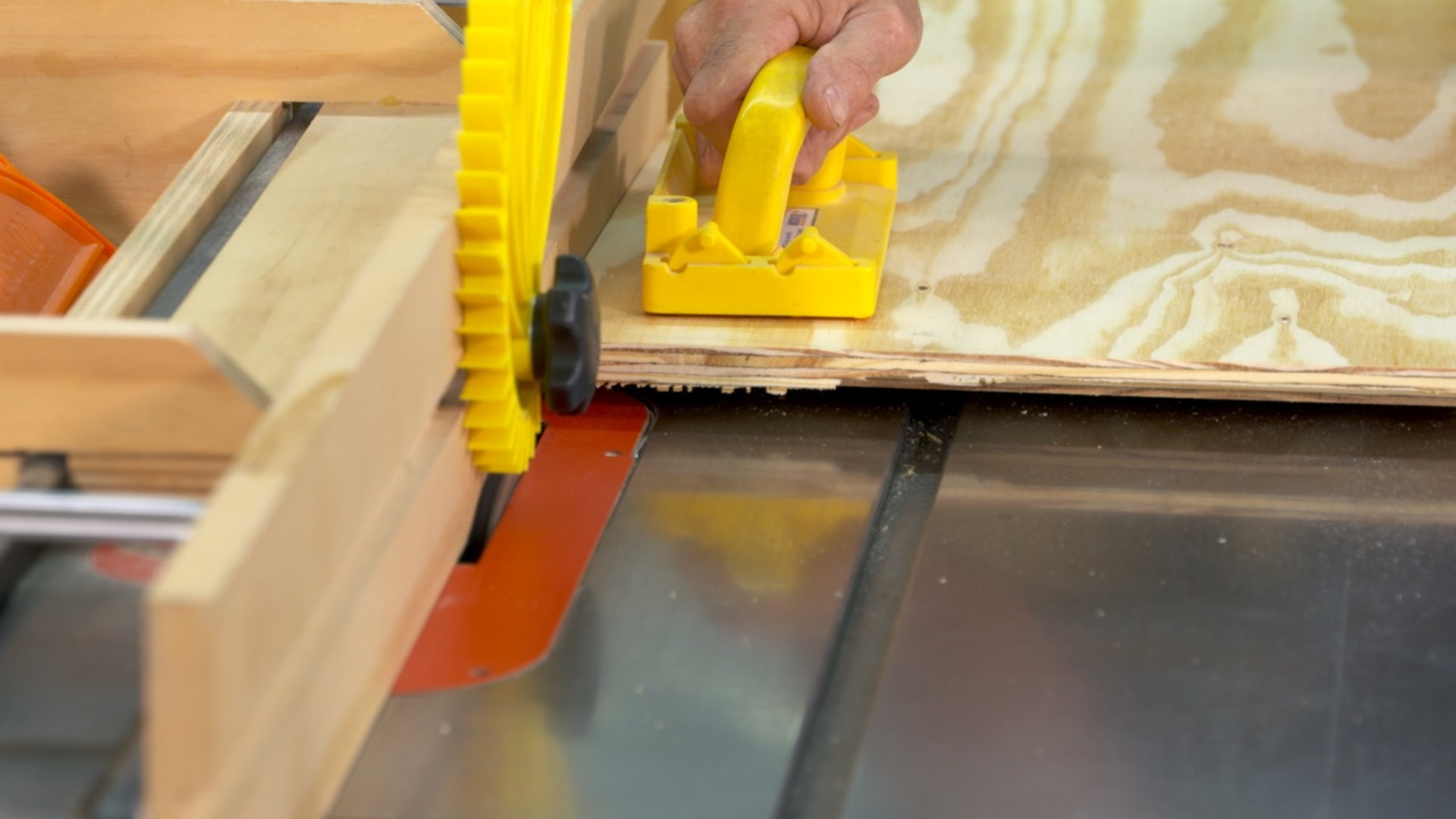
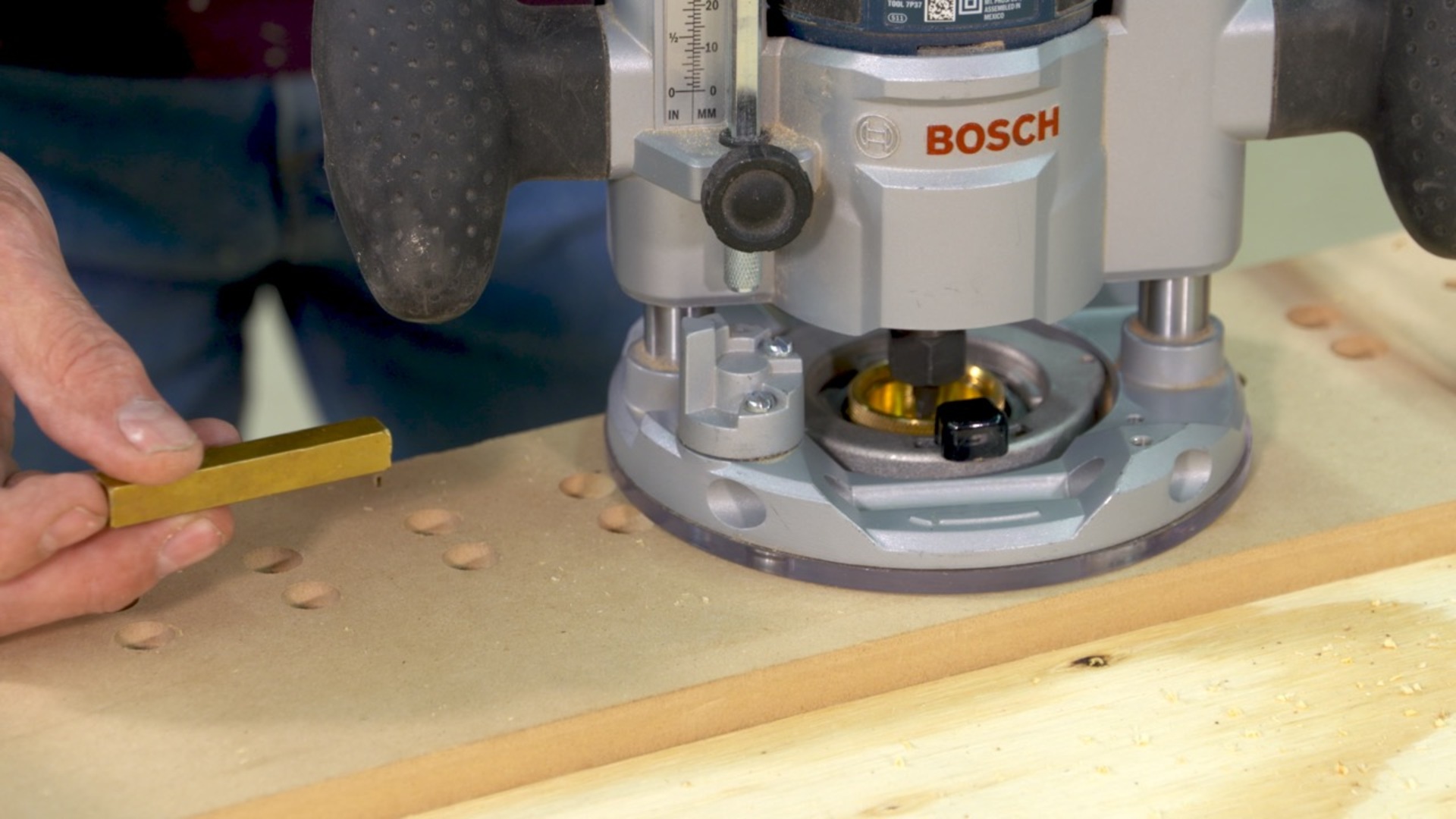
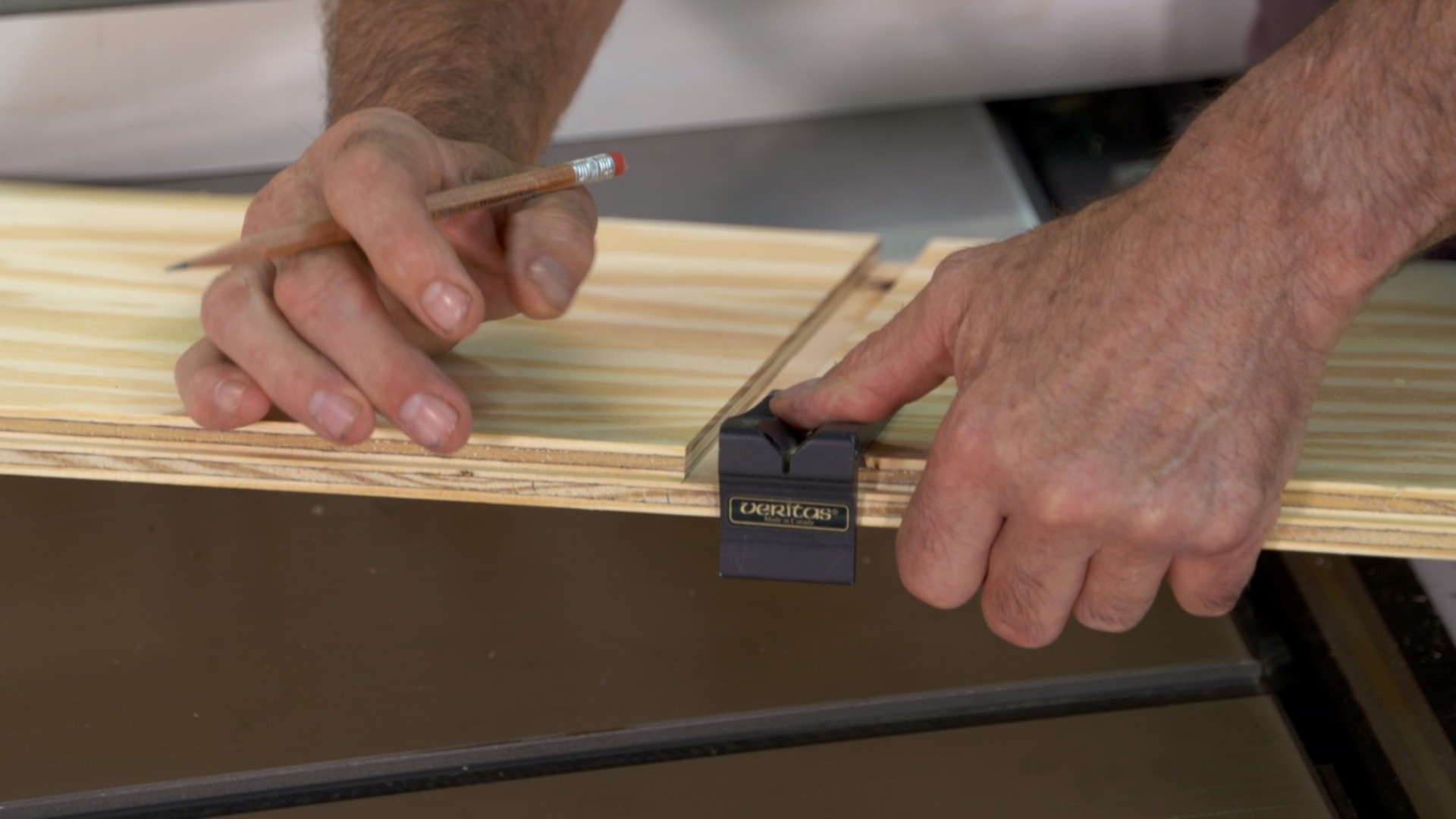
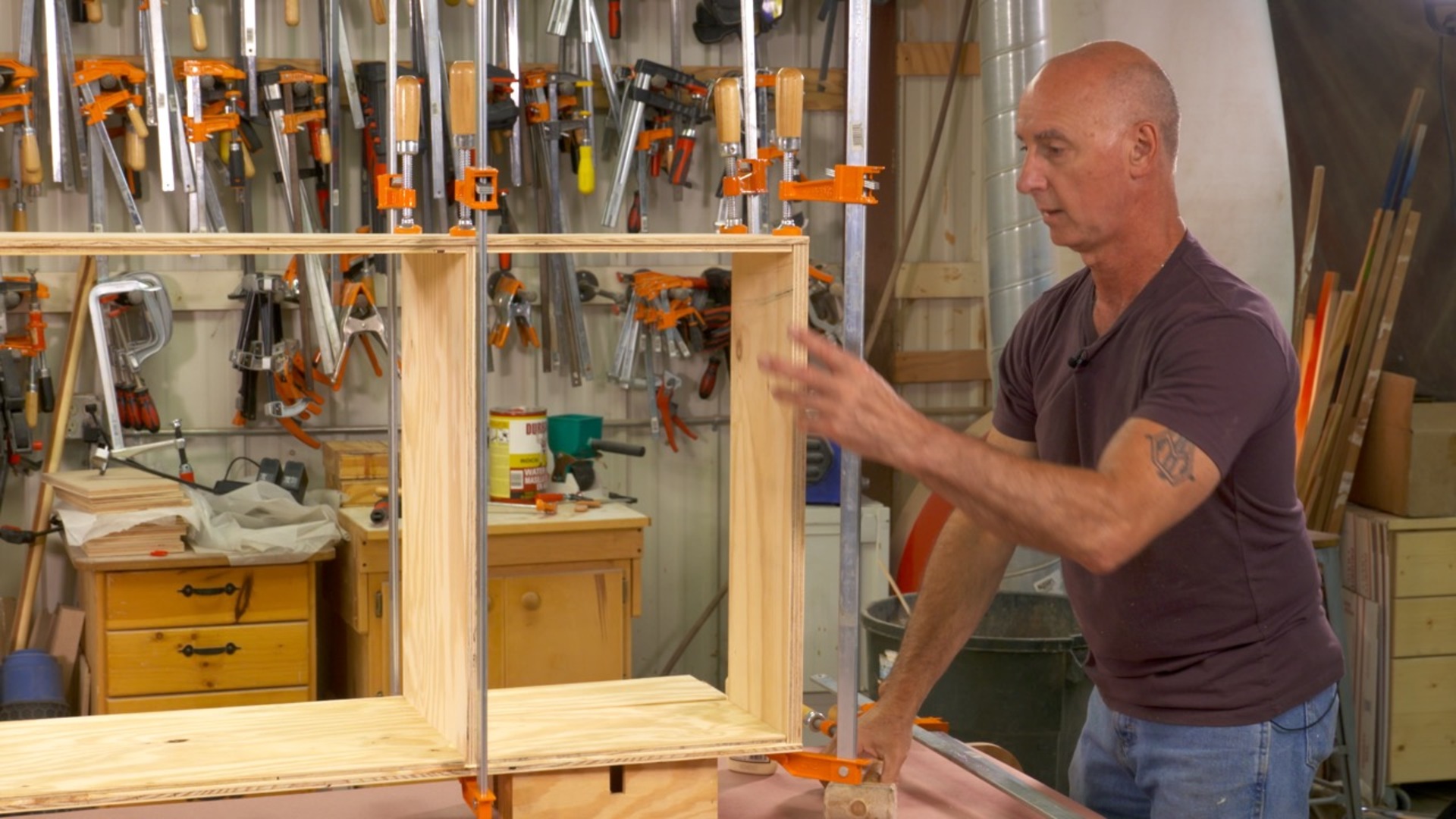
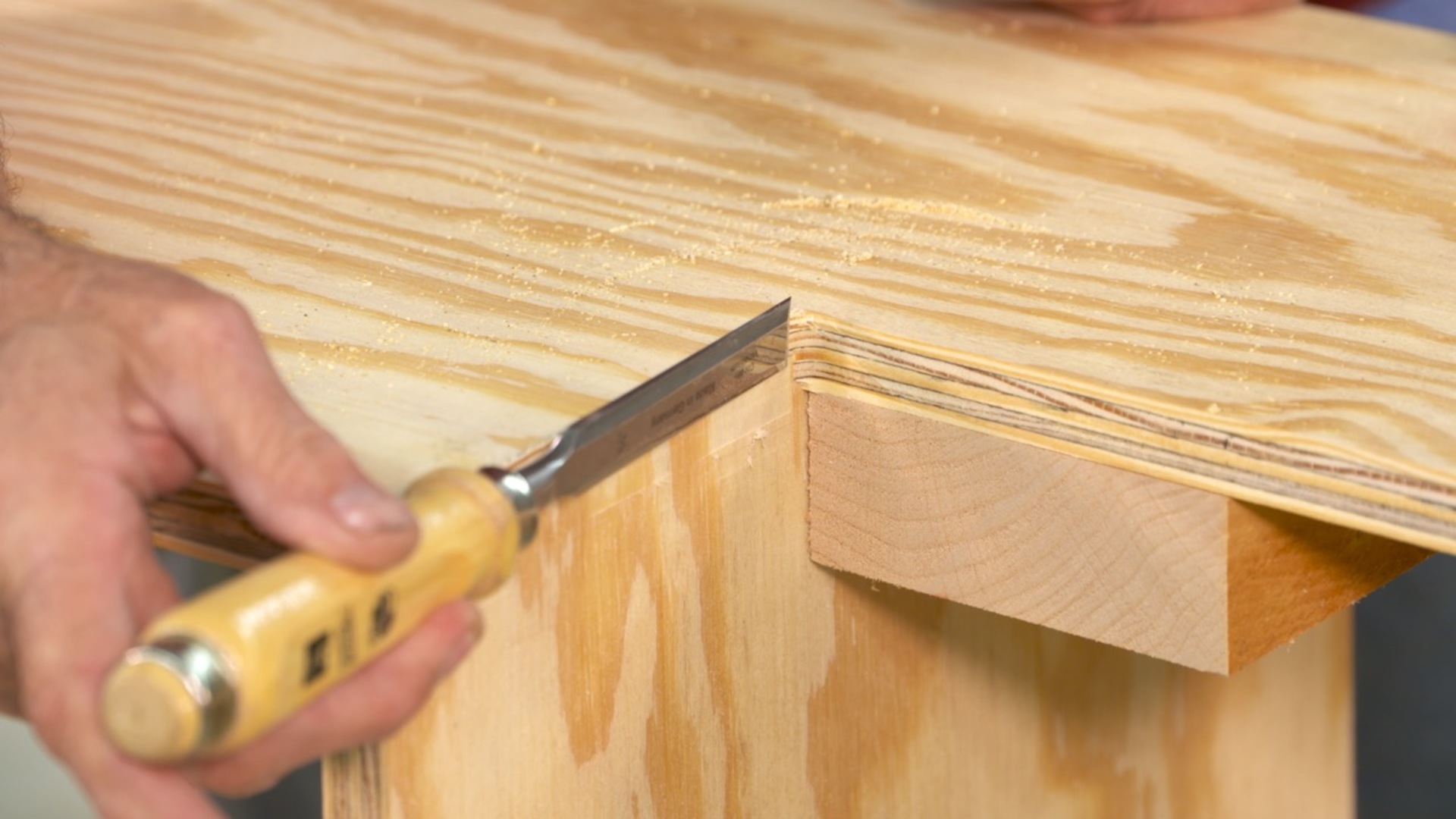
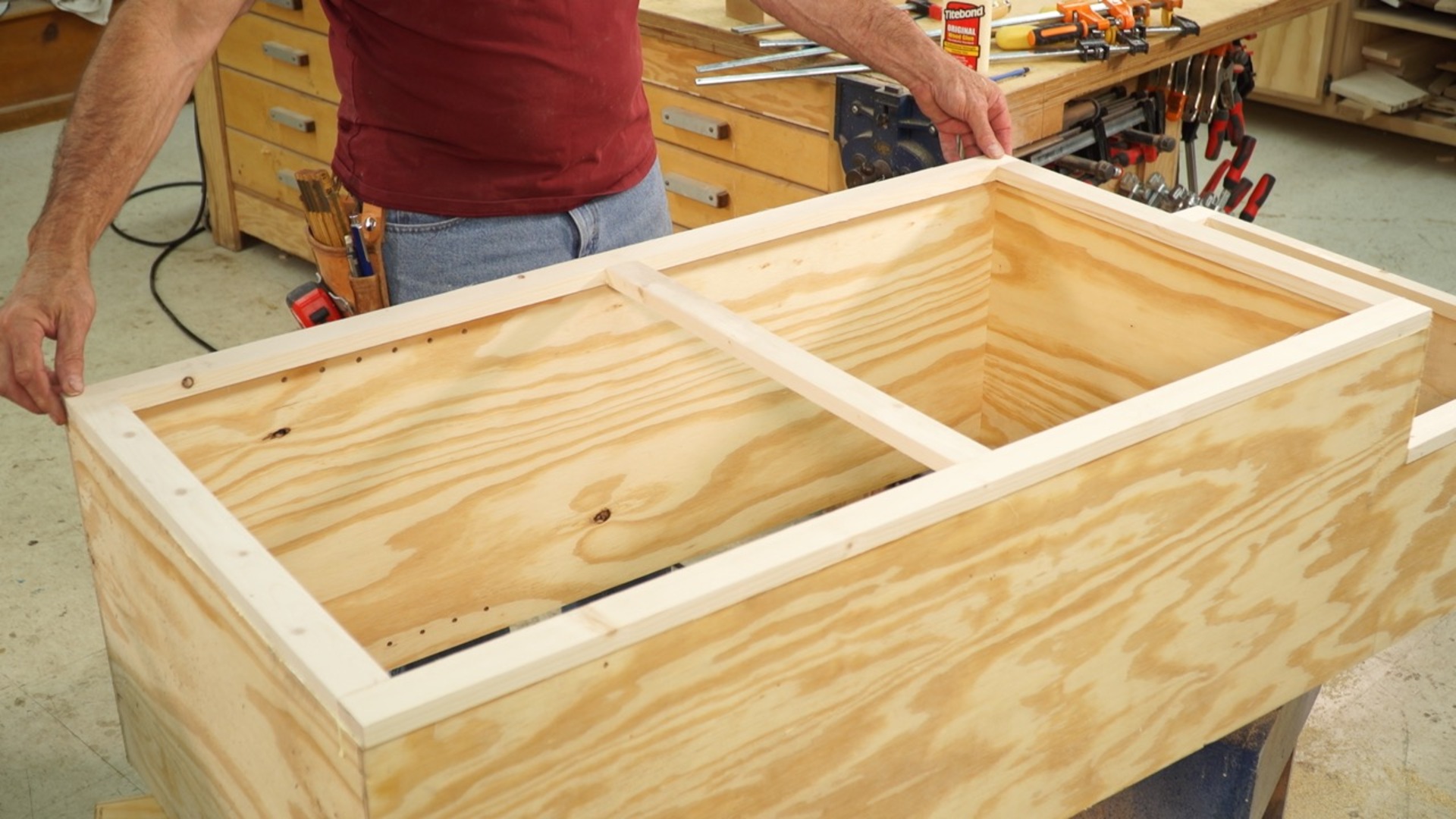
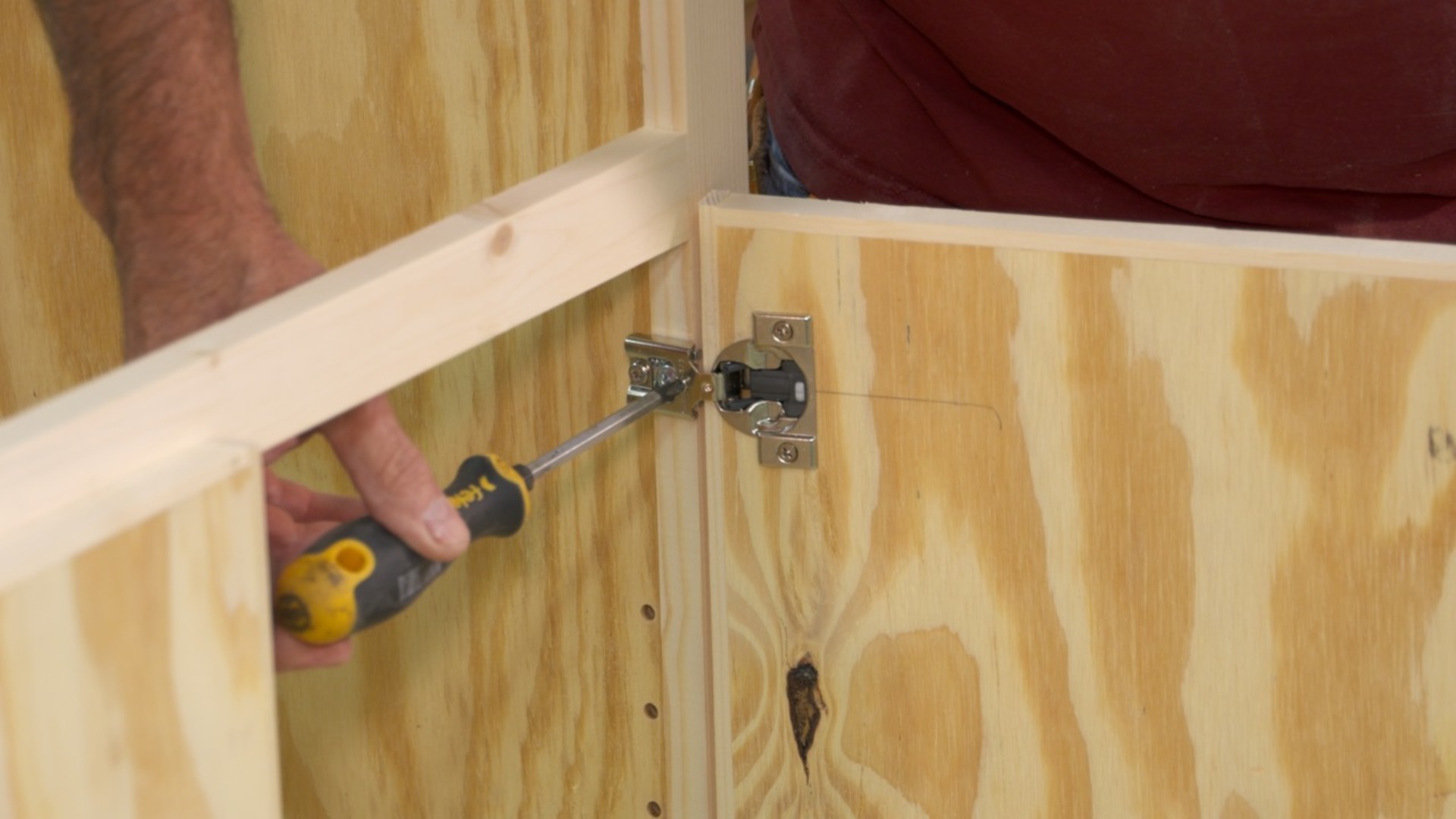
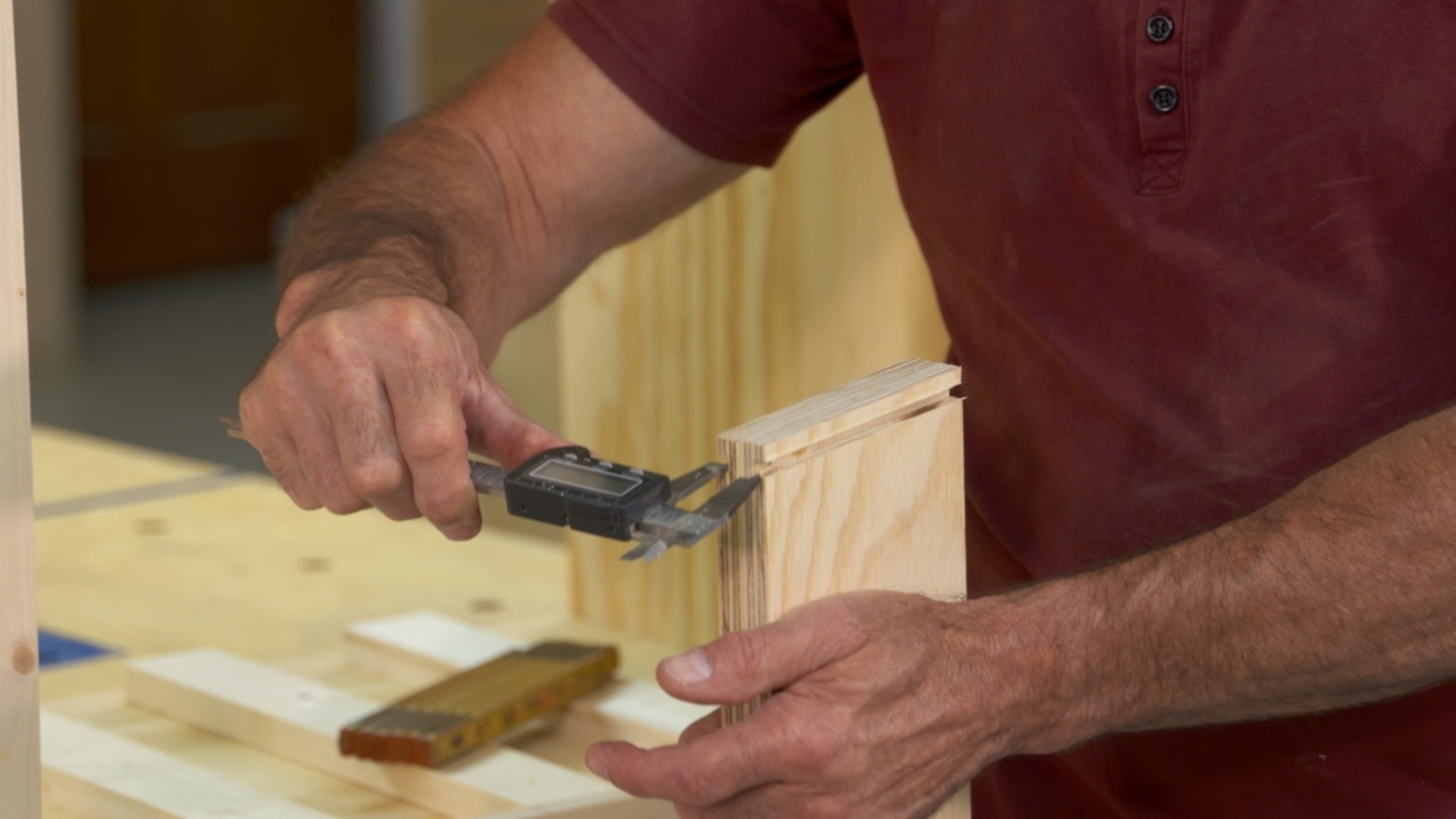
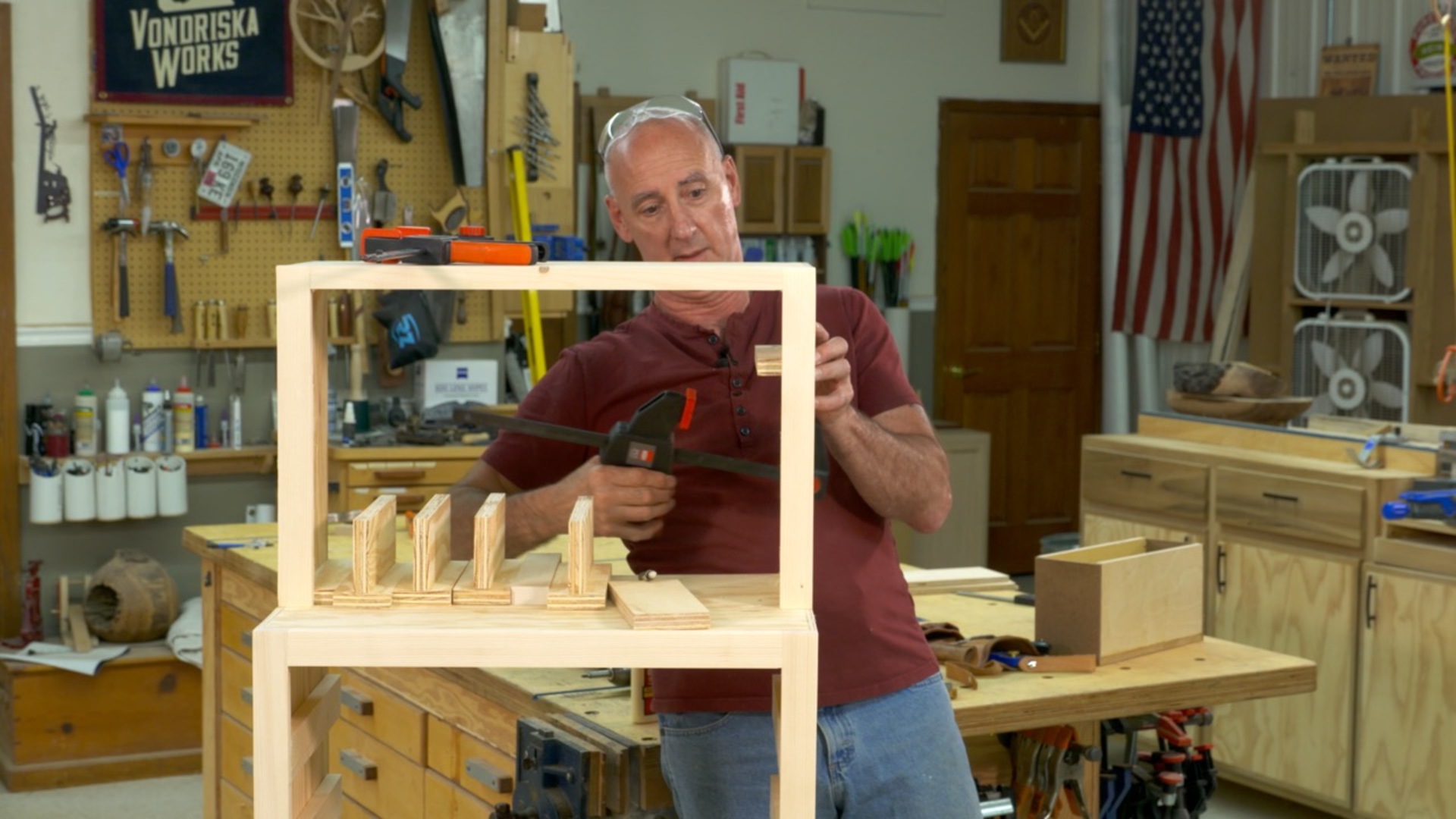
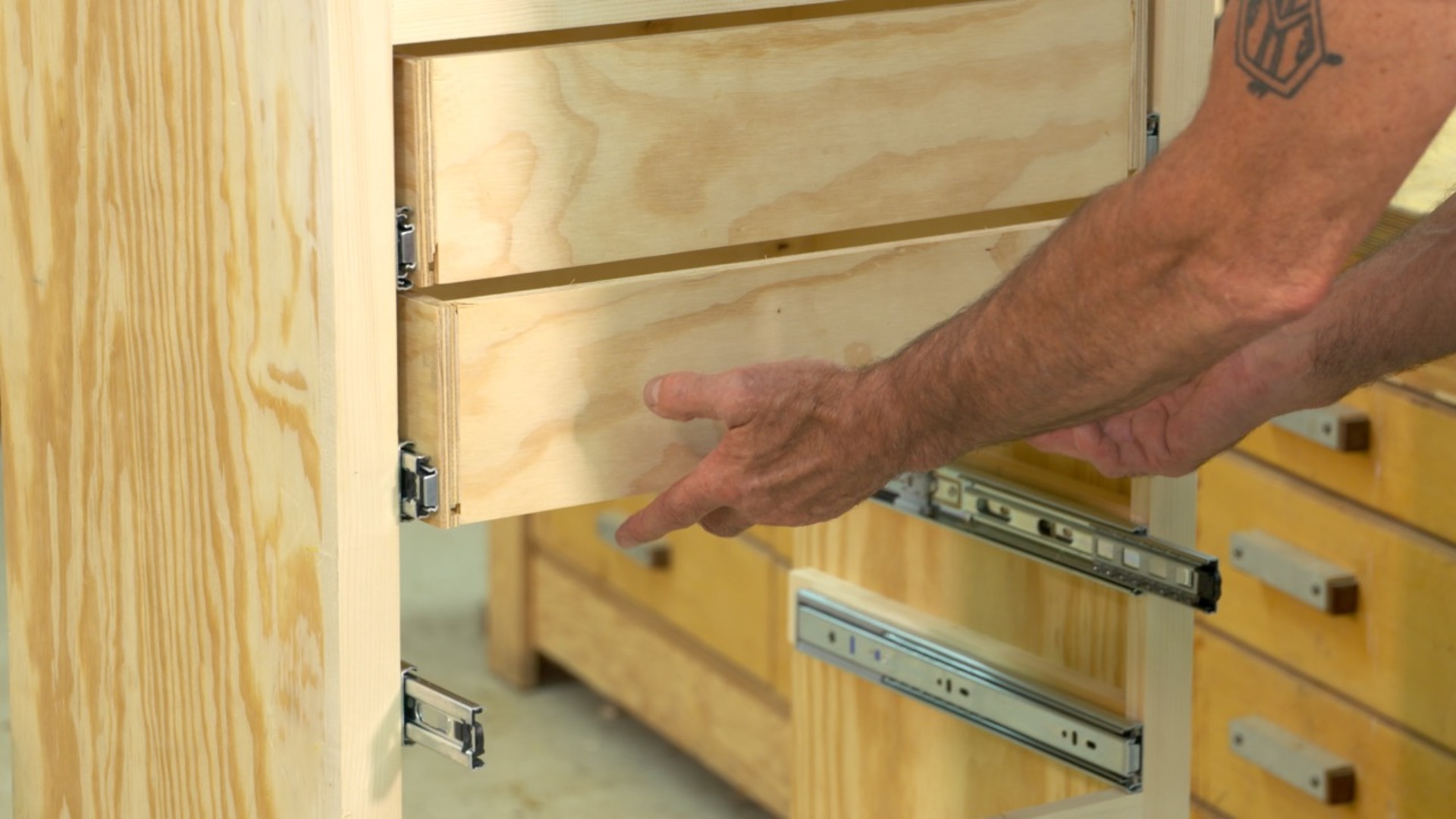
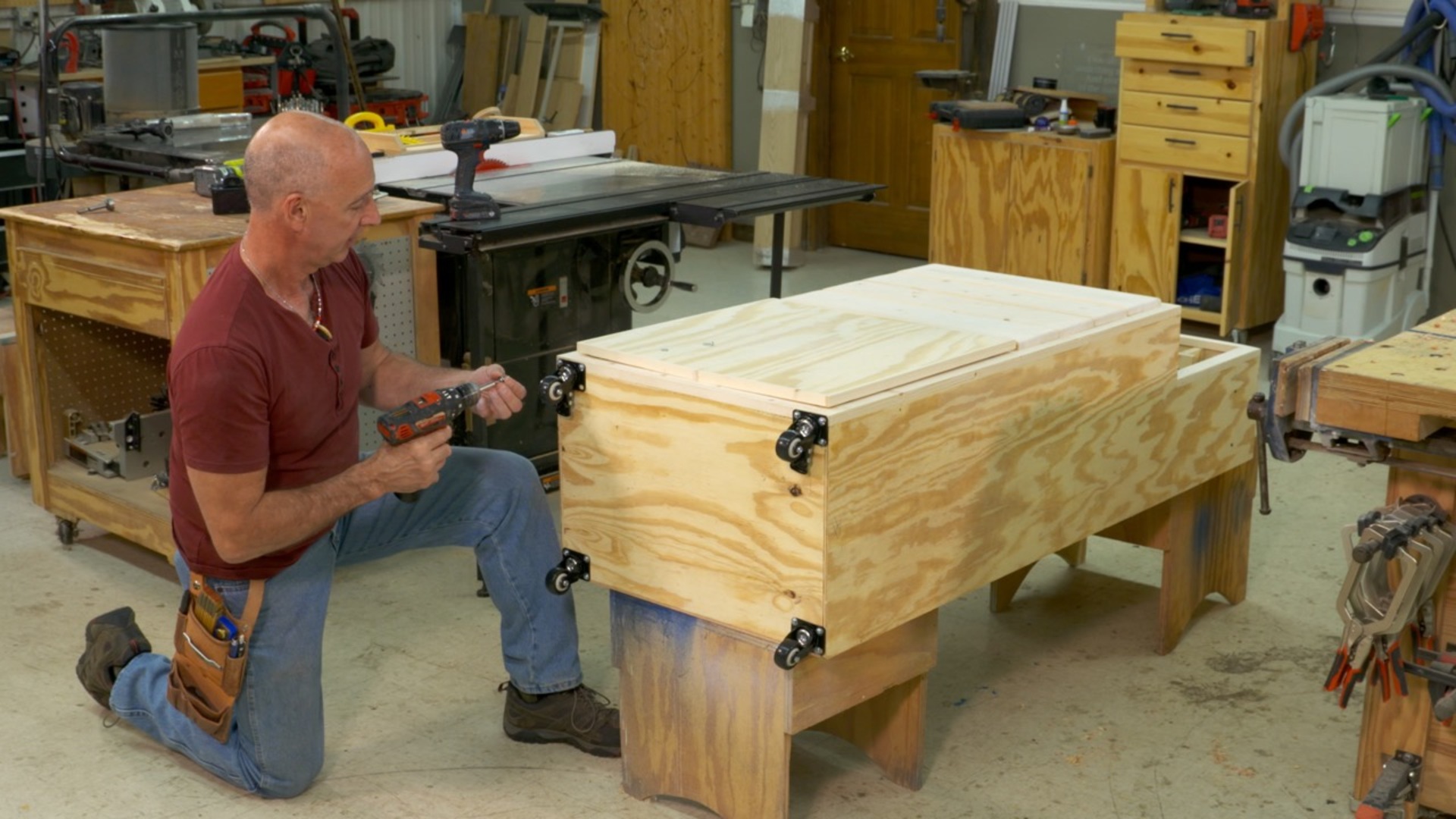
Cordless tools are becoming more and more prevalent in the shop. We’ve designed a task-specific tool station, just for your cordless tools. It provides hangers for your tools (the hangers also work well for pneumatic tools), a shelf where your chargers can live, drawers to hold your fasteners, and a two-door cabinet for larger tools.
This project consists of standard case joinery; dadoes and rabbets. The face frame is held together with pocket hole screws, and the drawer boxes are made with a lock rabbet joint. You can, of course, substitute other joinery methods for your project.
The Tool Station provides you with the opportunity to work with full extension drawer slides and European hinges, great hardware to be familiar with.
George Vondriska
Formally trained in technology education, George Vondriska has been teaching woodworking since 1986. He has been the managing editor of Woodworkers Guild of America since 2007. In addition to classes at his own Vondriska Woodworks School, George teaches at woodworking shows across the country and has taught woodworking for the Peace Corps, Andersen Window, Northwest Airlines and the Pentagon.
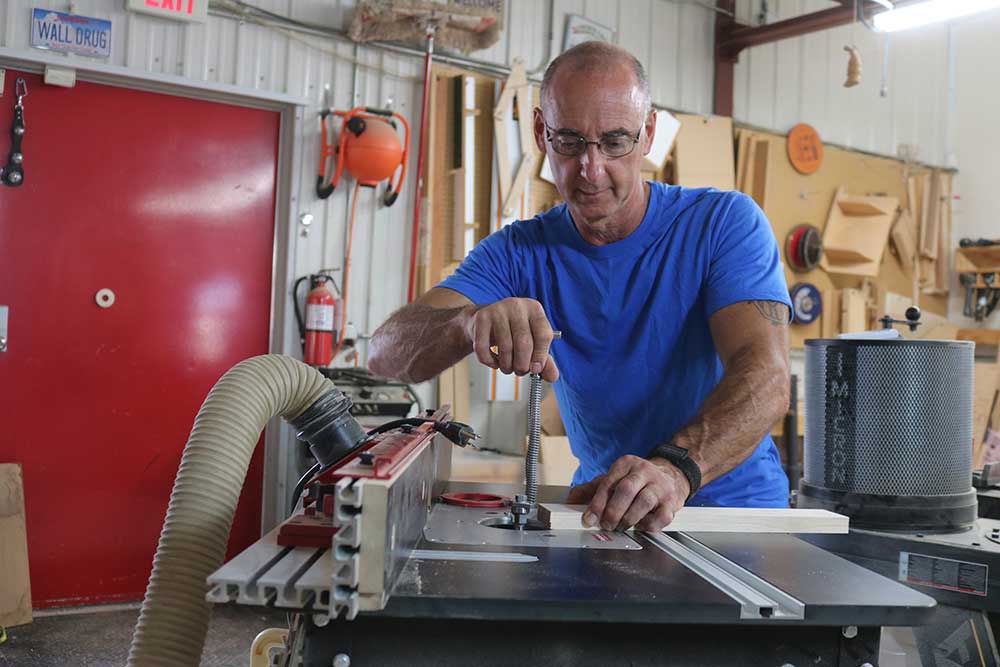
Bonus materials available after purchase