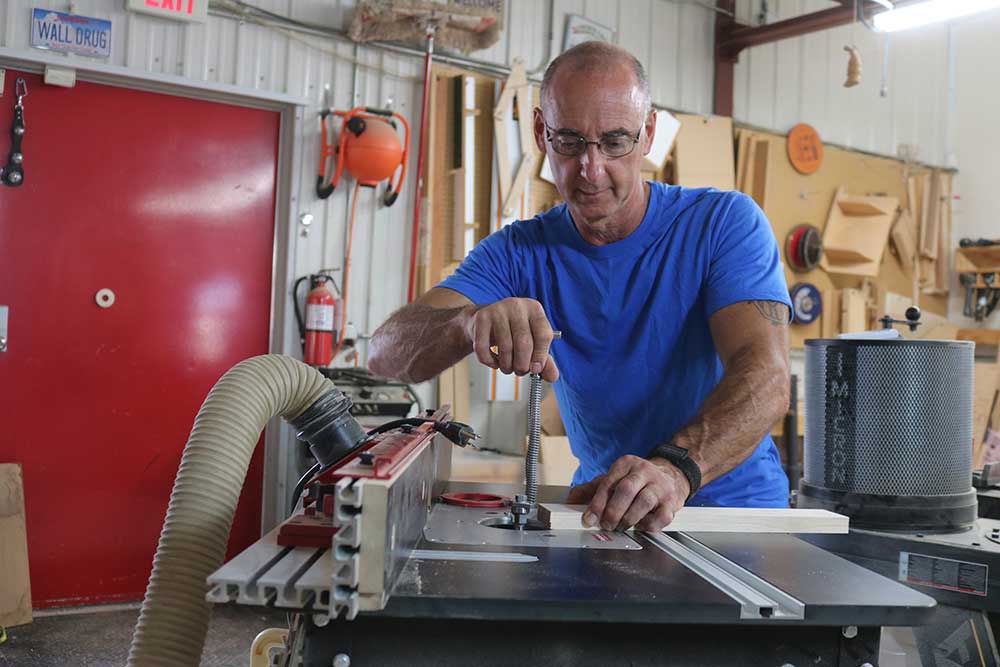
Build a Shave Horse
George Vondriska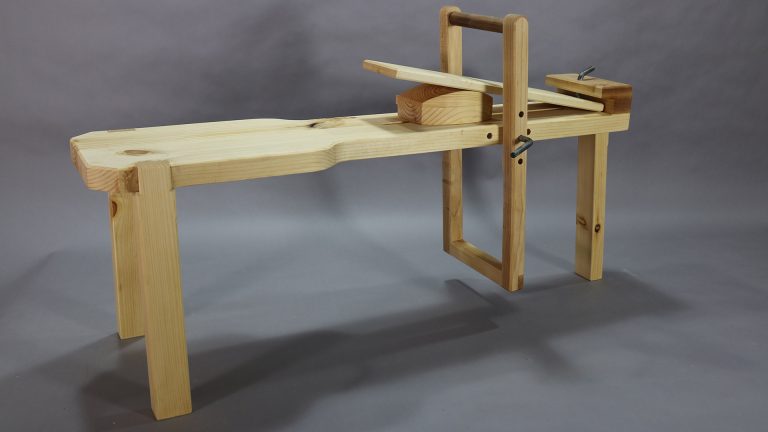
- In-depth Instruction; over 125 mins
- On-demand video access anytime
- Bonus downloadable PDF resources
- Access to class Q&A
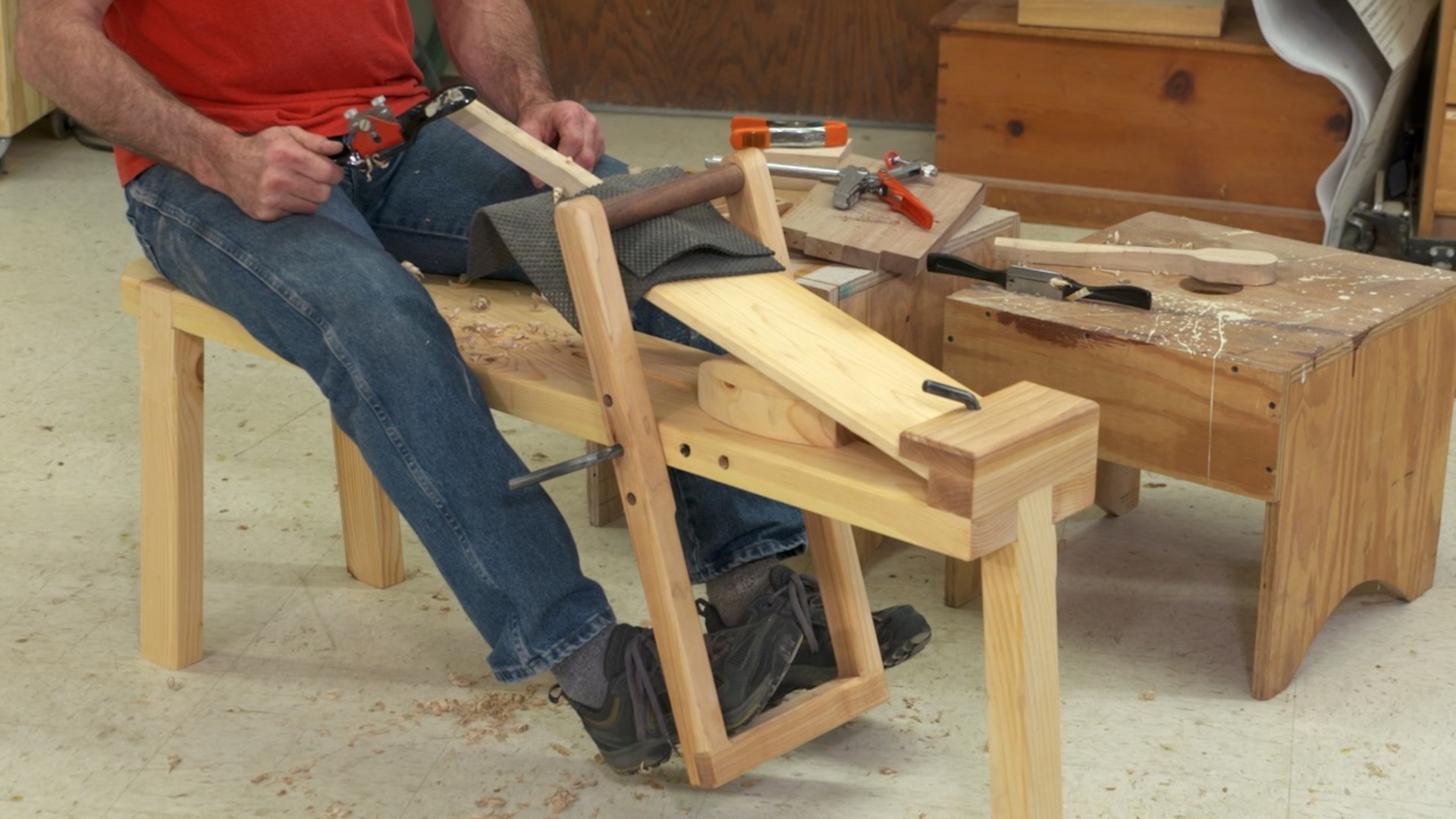
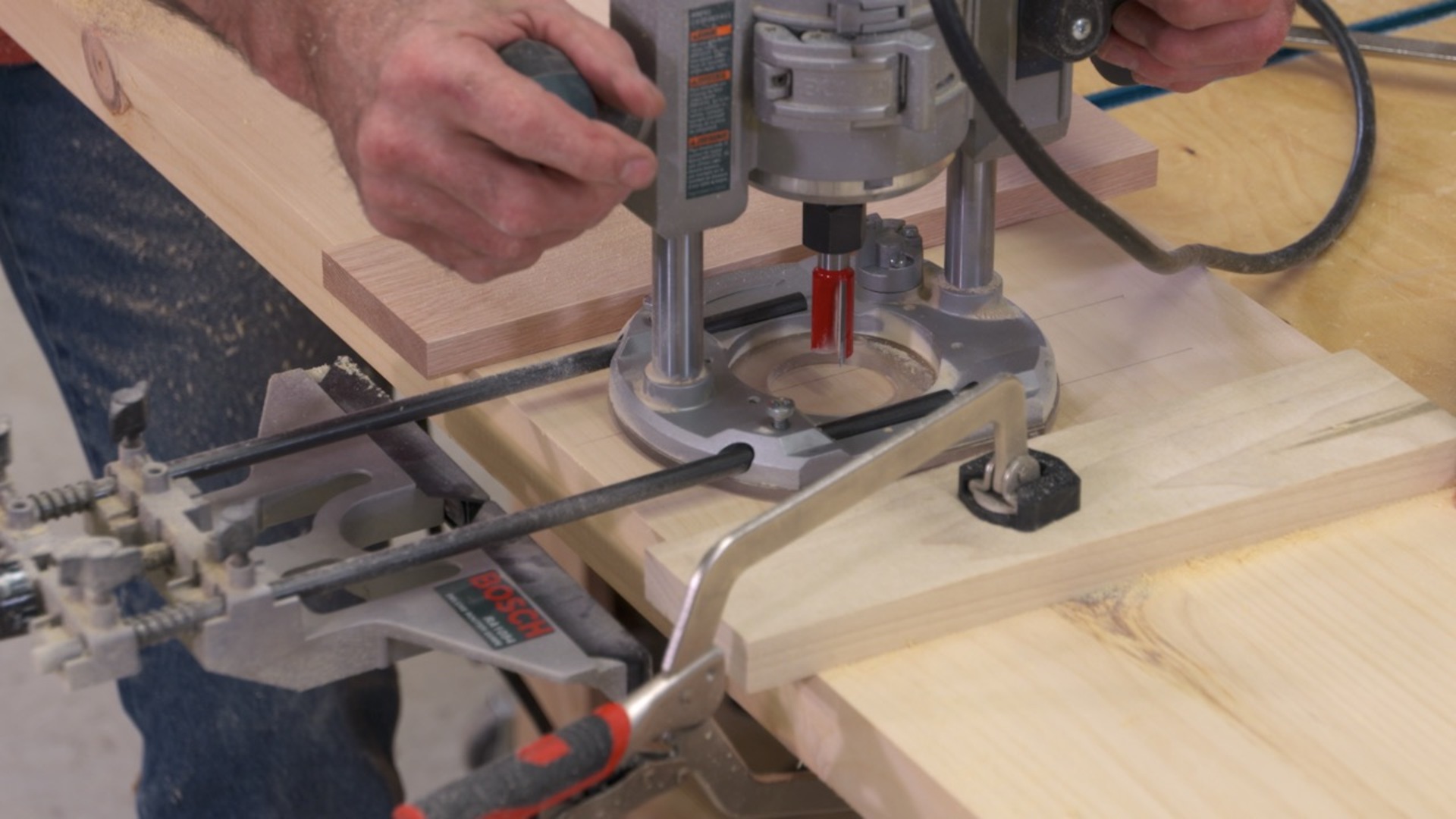
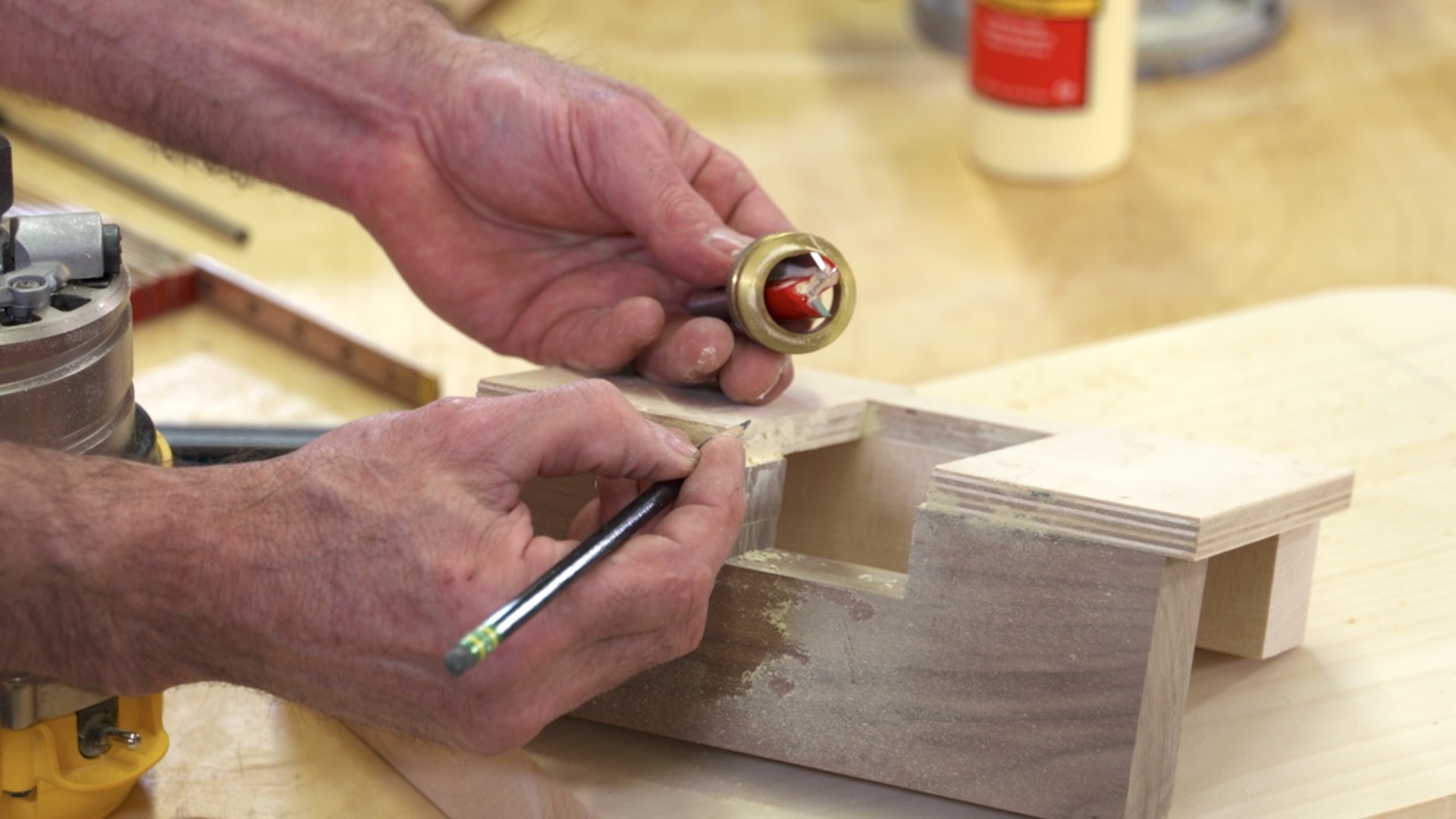
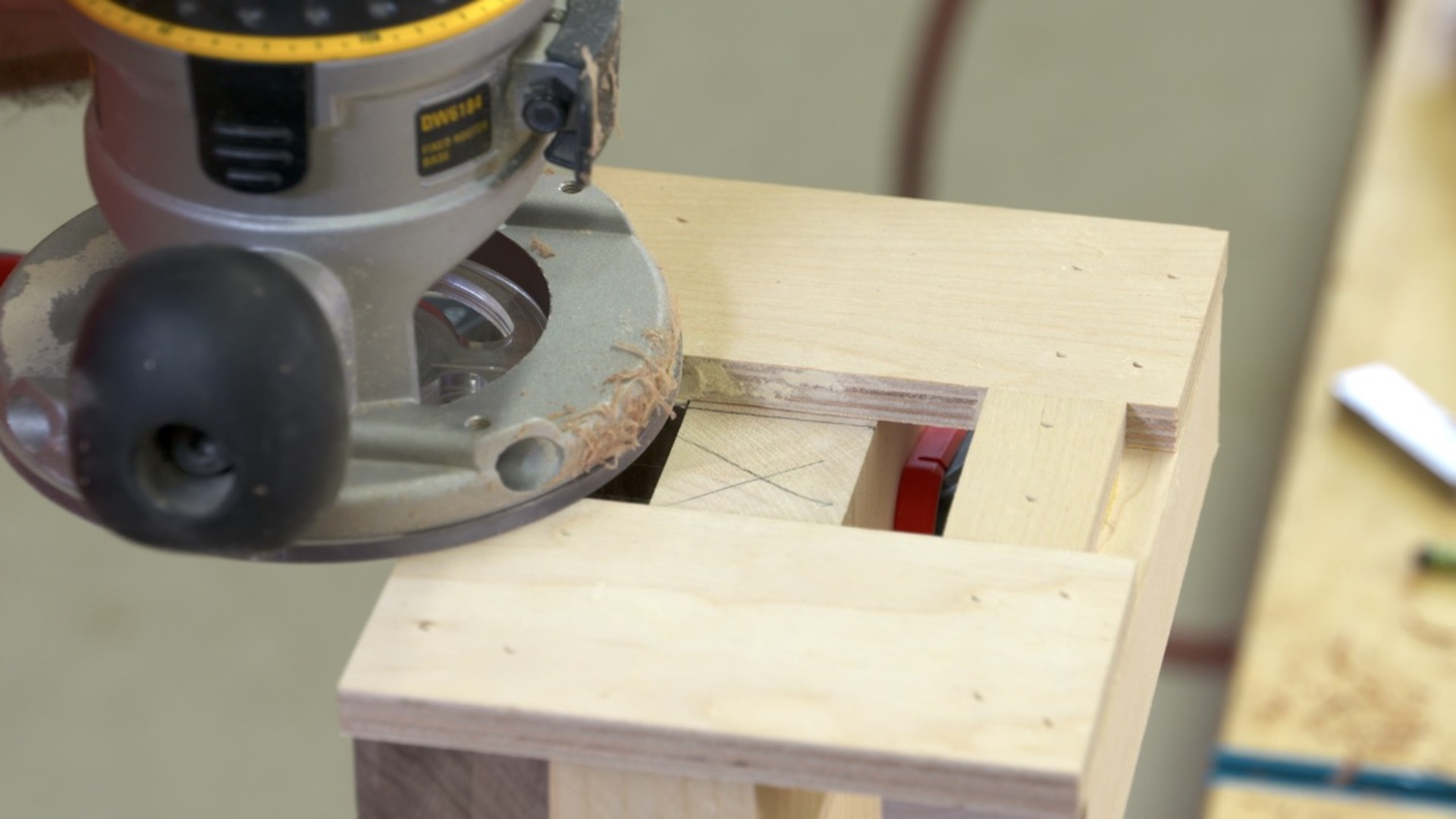
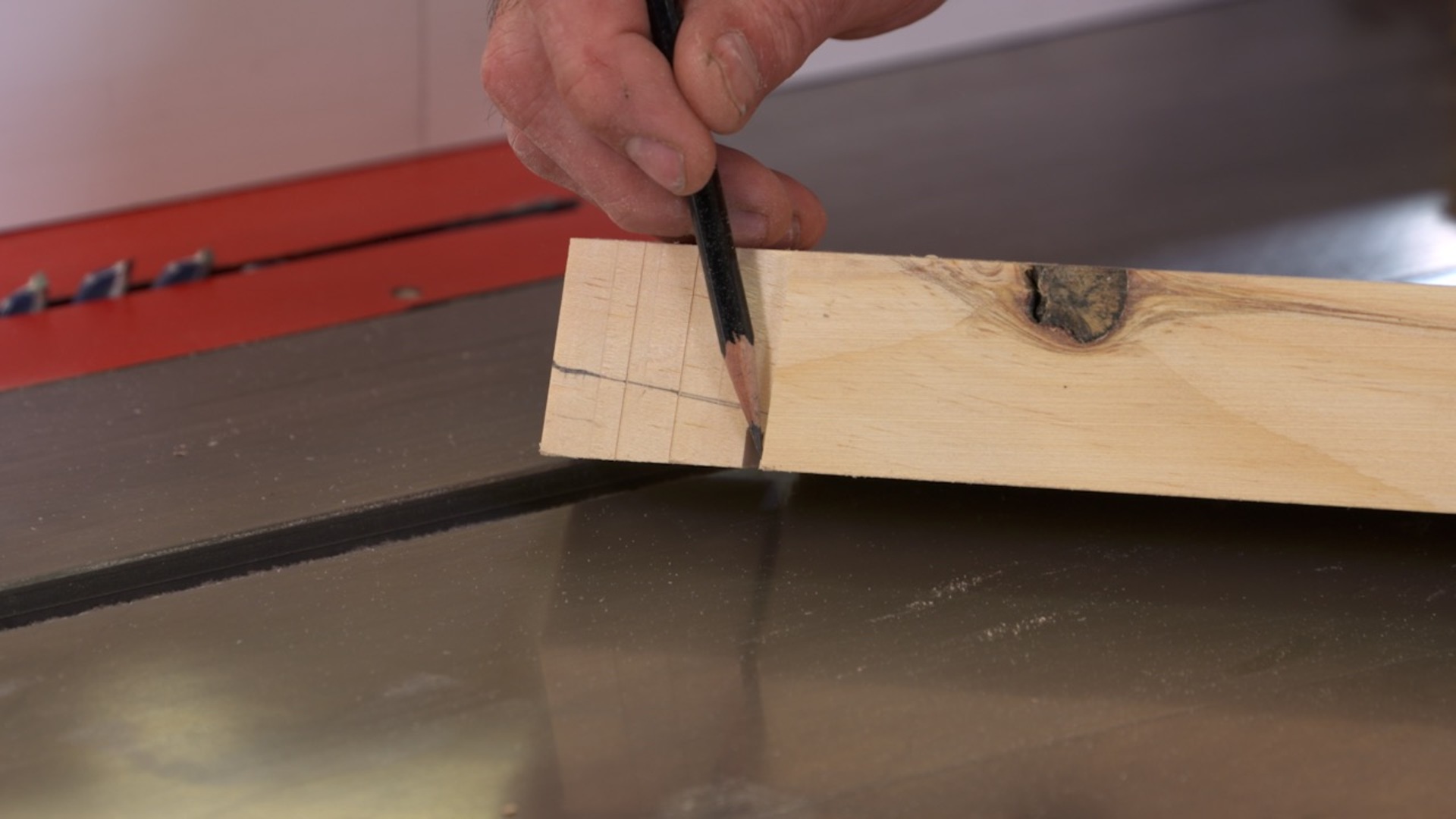
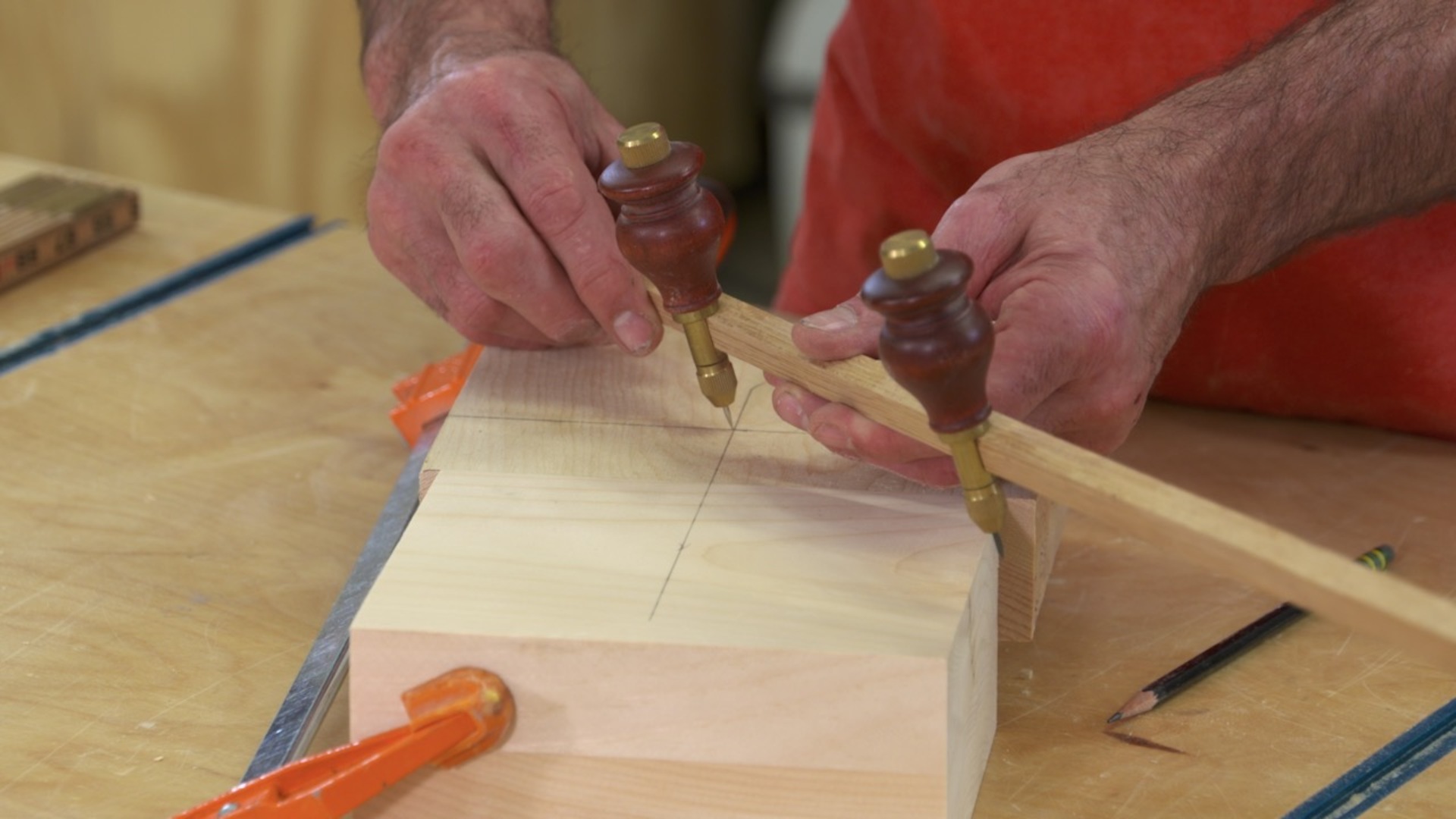
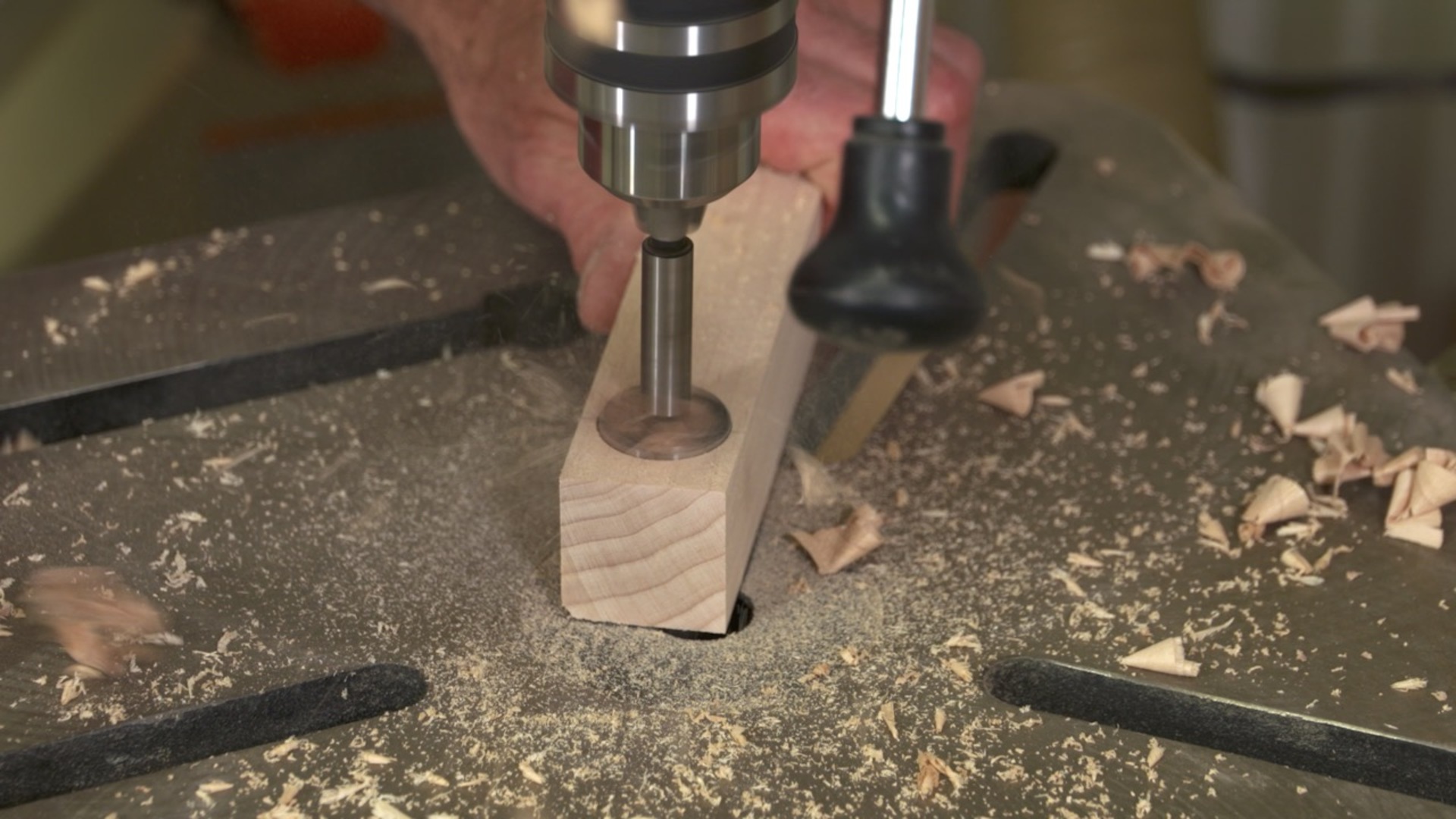
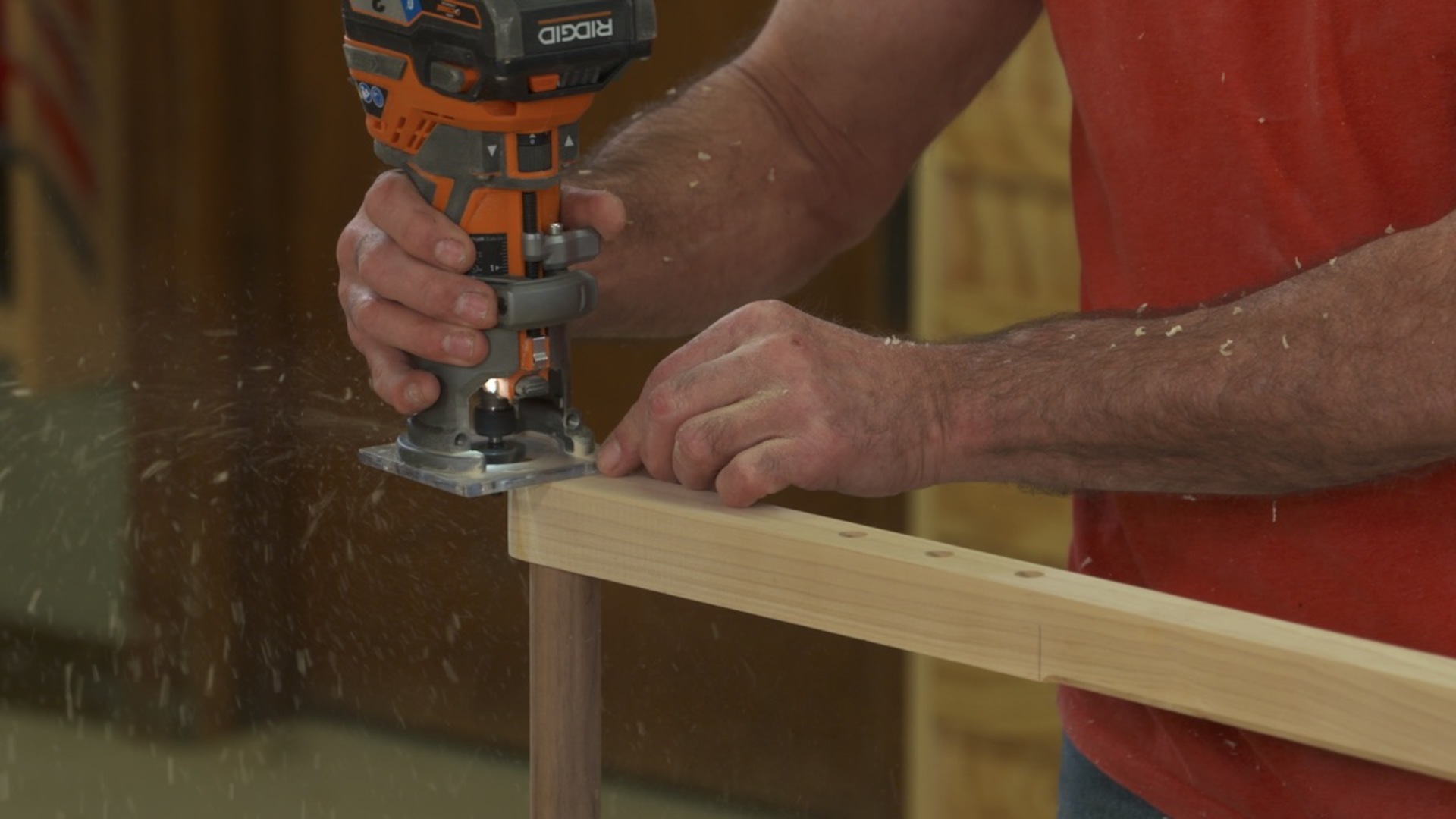
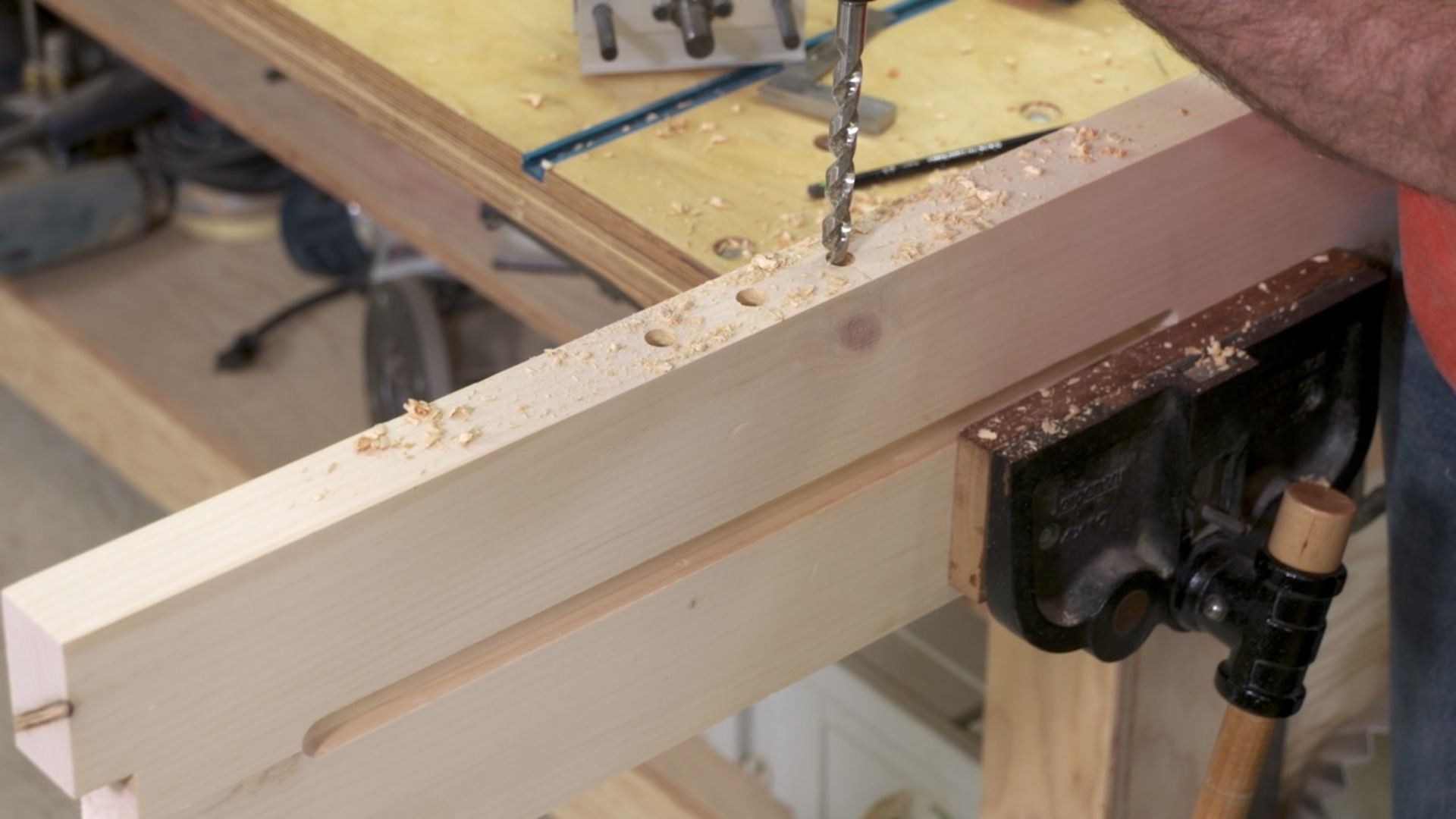
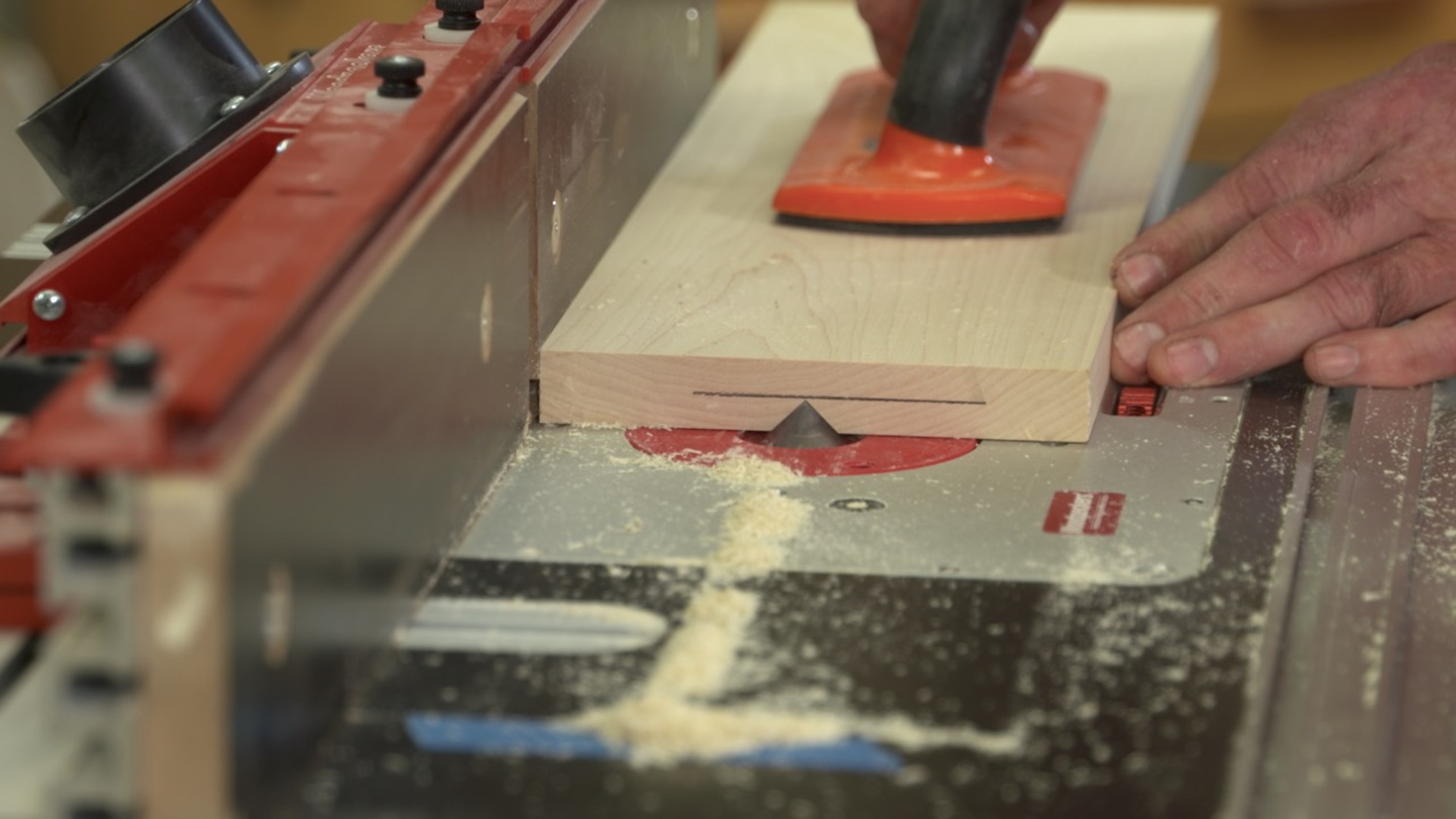
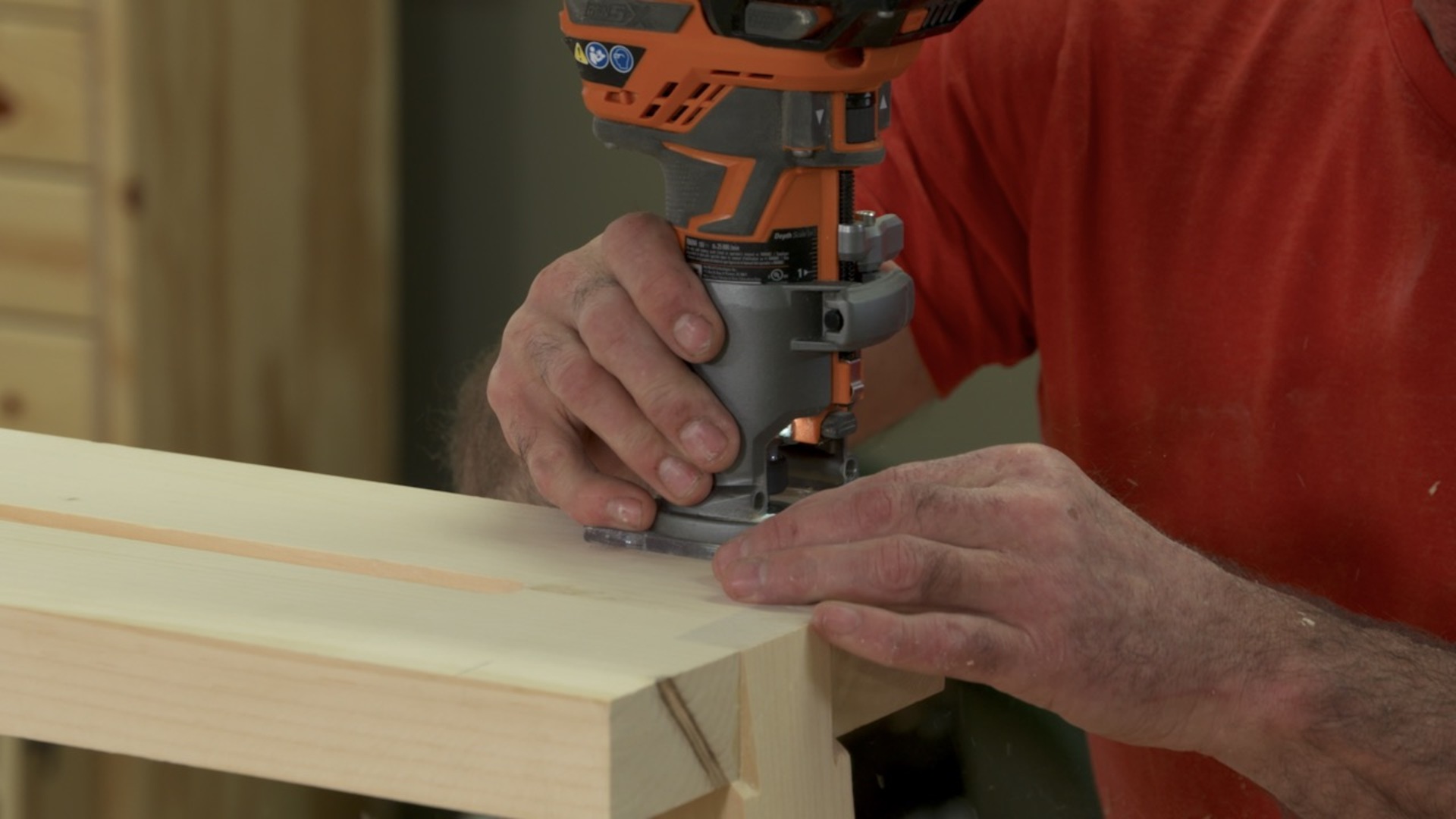
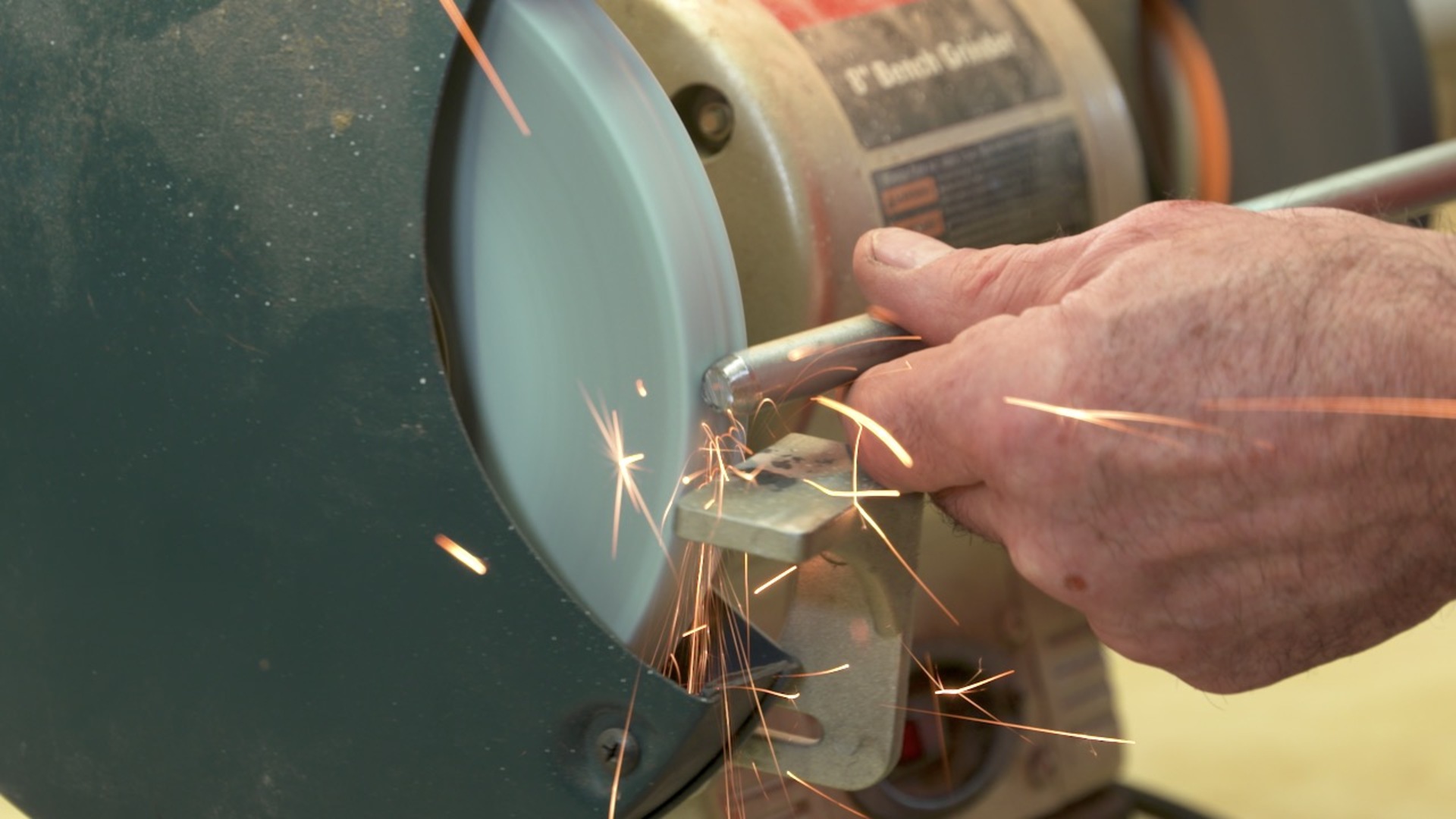

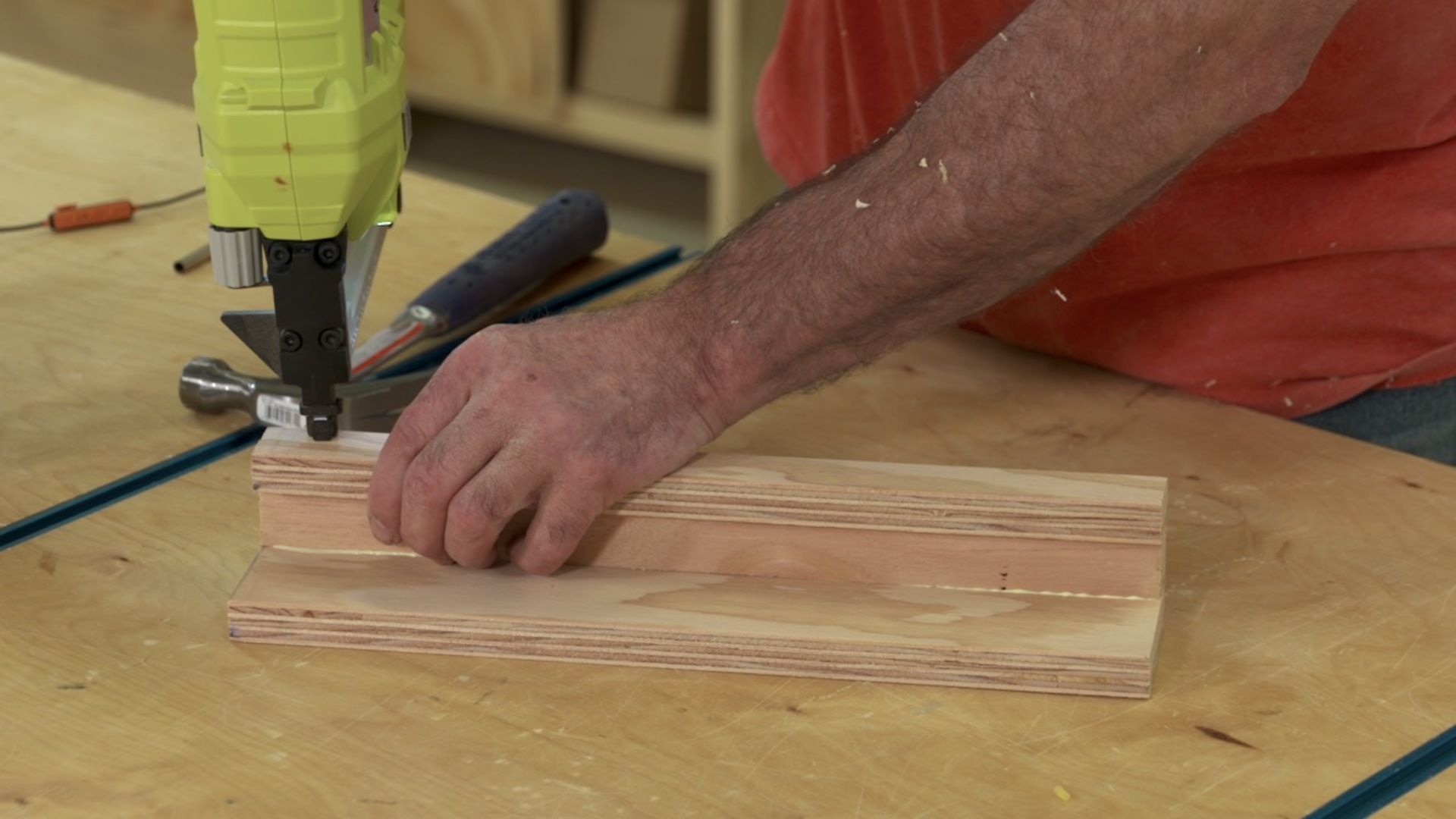
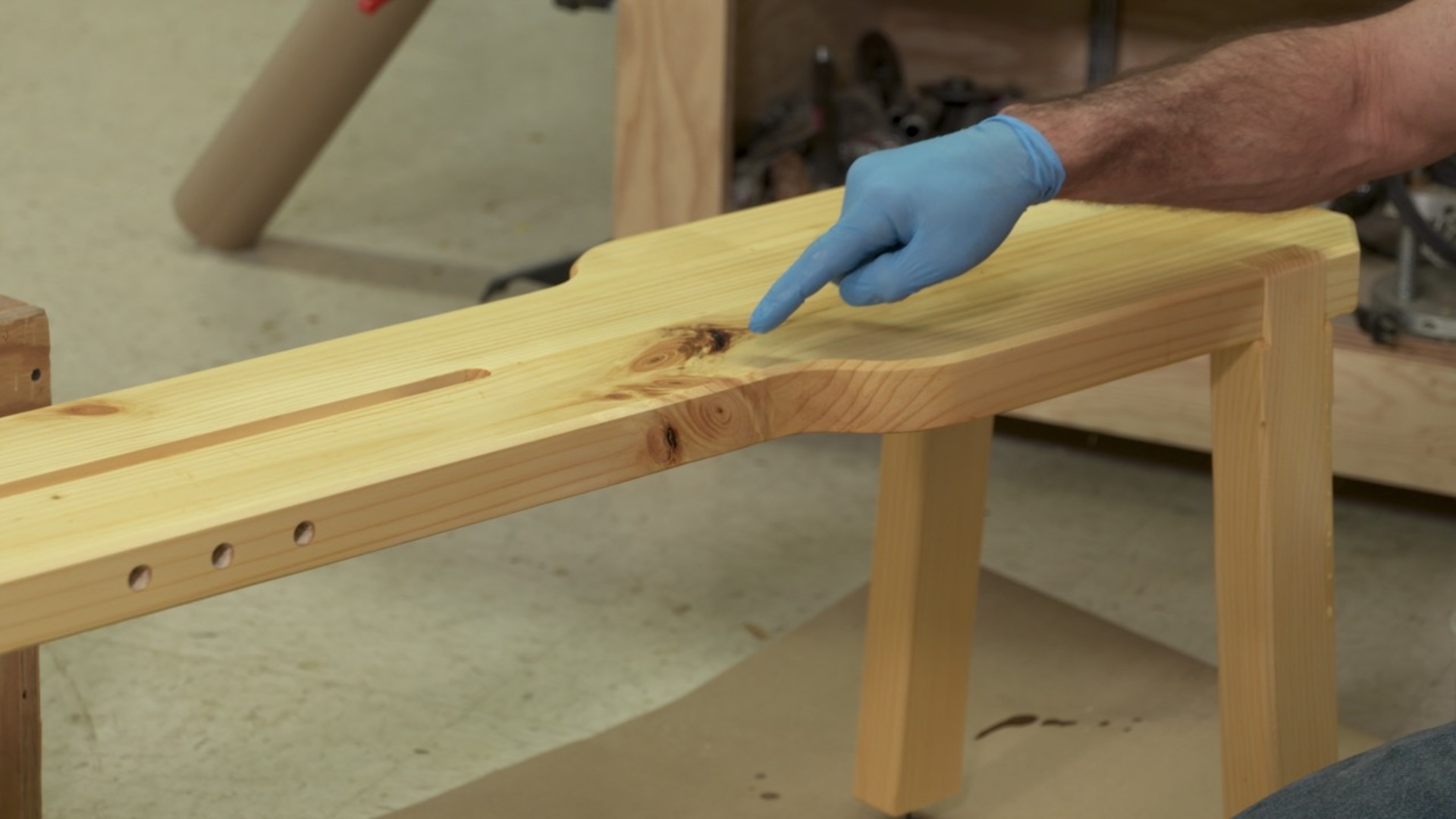
Cross a workbench with a vise, add in a few more features, and you end up with a shave horse. This is a workbench you sit on, and it includes a way to grip your material as you work on it.
Common shave horse projects
A shave horse is typically used by people who are carving or doing with a drawknife or spokeshave. Your workpiece is held in place by pressure from your foot so it’s very easy to carve, reposition, carve, reposition. And, because you’re sitting in front of your workpiece, the body mechanics of using a spokeshave or drawknife are great.
You’ll see a shave horse used for everything from traditional bows to spoons to tool handles to table legs, and more.
Features
In addition to the traditional characteristics found in a shave horse, this version includes another hold down that allows you to clamp work to the seat. This is very handy and allows you to use this shave horse for many more projects.
What you’ll learn
A unique woodworking task on this project is fitting the tenons on the legs to the mortises in the seat. The legs are splayed at an angle, so it takes finessing of the tenon to create a sound fit.
The seat transitions from wide to narrow through an S curve. You’ll create the flowing curve by drawing and cutting tangential circles.
The project includes a half lap joint. This is a great joint to learn because of its strength.
George Vondriska
Formally trained in technology education, George Vondriska has been teaching woodworking since 1986. He has been the managing editor of Woodworkers Guild of America since 2007. In addition to classes at his own Vondriska Woodworks School, George teaches at woodworking shows across the country and has taught woodworking for the Peace Corps, Andersen Window, Northwest Airlines and the Pentagon.
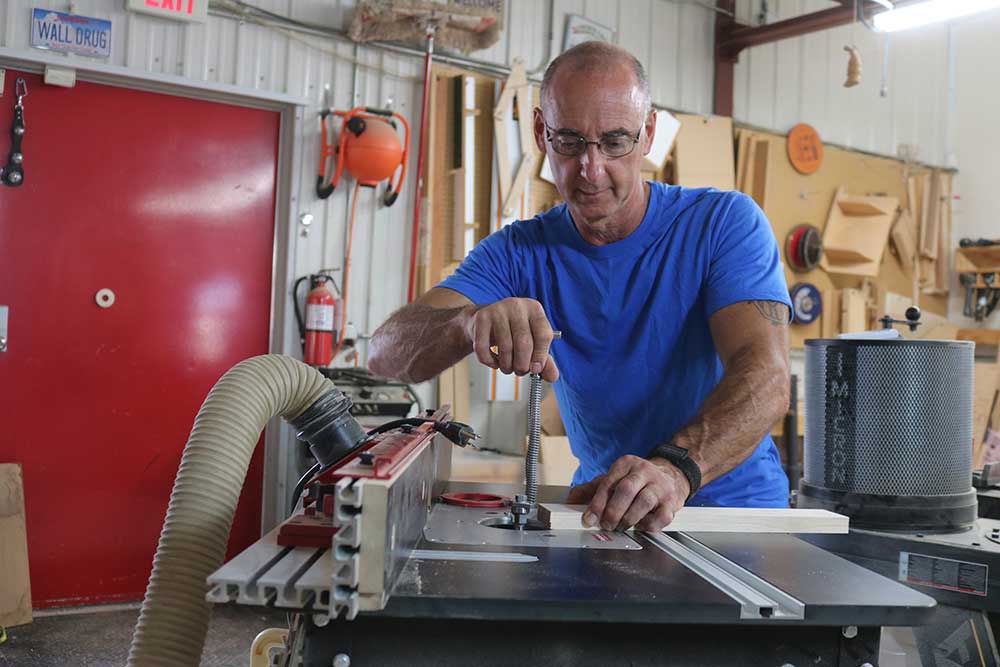
Bonus materials available after purchase